Explore the essential guide to finding reliable aero parts suppliers, with insights into the aircraft parts distribution landscape, evaluation criteria for trustworthy aerospace components suppliers, and practical tips for navigating the complexities of the aviation supply chain. Learn about the importance of quality certifications, industry reputation, and the key players in the market to ensure you source the most reliable airplane spare parts for sale. Perfect for aviation professionals seeking to enhance their commercial aviation spares procurement strategy.
Section I. Introduction
- The Importance of Reliability in Aero Parts Supply
- Summary: Discusses the critical nature of reliability in the aerospace industry and its impact on safety, efficiency, and operational success.
- Challenges in Finding Trustworthy Suppliers
- Summary: Explores common obstacles faced by buyers, including market saturation, varying quality standards, and the complexity of verifying supplier credibility.
Section II. Understanding Aircraft Parts Distribution
- Overview of the Distribution Landscape
- Summary: Provides an insight into how aircraft parts distribution works, including the roles of OEMs, distributors, and third-party vendors.
- Key Players in the Market
- Summary: Highlights major distributors, OEMs, and aftermarket suppliers that have established a reputation for reliability and quality.
Section III. Criteria for Evaluating Reliable Aerospace Components Suppliers
- Quality Certifications and Standards
- Summary: Emphasizes the importance of industry certifications (e.g., AS9120, ISO 9001) in assessing supplier reliability.
- Track Record and Industry Reputation
- Summary: Discusses how a supplier’s history and reputation in the industry can be a reliable indicator of their dependability and quality of service.
- Supply Chain Transparency and Ethical Sourcing
- Summary: Explores the significance of transparent supply chains and ethical sourcing practices in ensuring component reliability.
Section IV. Navigating Online Aircraft Parts Stores
- Benefits and Pitfalls
- Summary: Analyzes the advantages of using online platforms for parts procurement and the potential risks involved.
- How to Vet an Online Store
- Summary: Offers practical tips for verifying the credibility and reliability of online aircraft parts suppliers.
Section V. Strategies for Securing Commercial Aviation Spares
- Building Long-Term Supplier Relationships
- Summary: Discusses the benefits of developing strong, long-term partnerships with suppliers for better reliability and service.
- Leveraging Technology for Better Sourcing
- Summary: Examines how modern technologies, like blockchain and AI, can improve the sourcing process and ensure the authenticity of parts.
Section VI. Conclusion
- The Future of Aircraft Parts Sourcing
- Summary: Speculates on future trends in the industry, including digital transformation and the increasing importance of sustainability in sourcing decisions.
Introduction
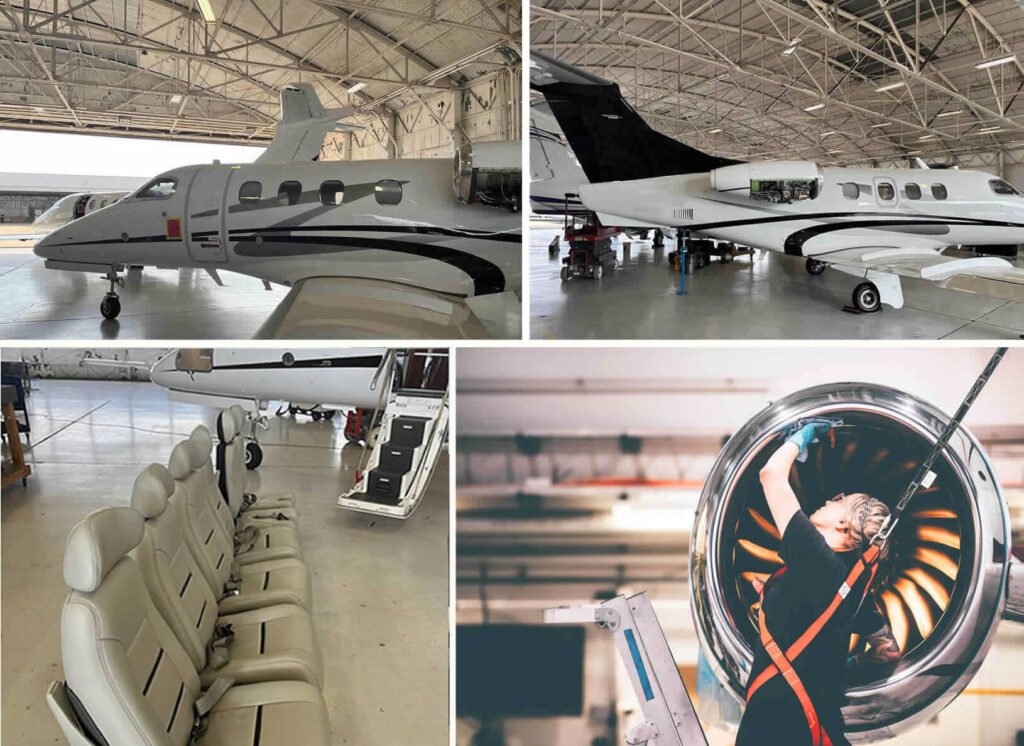
The Importance of Reliability in Aero Parts Supply
Reliability: A Cornerstone of Aviation Safety
In the realm of aviation, the reliability of aero parts is not just a preference; it’s a fundamental necessity. The safety of countless passengers and the integrity of multi-million-dollar machinery hinge on the quality and dependability of every single component, from the smallest screw to the largest turbine engine. This section underscores the critical role that reliable aerospace components play in ensuring operational success and safety in the skies. The aviation industry’s stringent standards reflect the non-negotiable demand for precision and reliability, making the selection of suppliers a matter of paramount importance.
Challenges in Finding Trustworthy Suppliers
Navigating the Complex Aerospace Supply Chain
The aerospace supply chain is a complex and multifaceted ecosystem, teeming with suppliers, distributors, and manufacturers each claiming to offer the pinnacle of reliability and quality. However, the reality of finding a supplier that consistently meets these claims is fraught with challenges. This paragraph delves into the difficulties of discerning quality amidst a saturated market, the intricacies of verifying supplier credibility, and the constant evolution of industry standards. It highlights the importance of due diligence and the need for buyers to be well-informed and strategic in their sourcing decisions.
FAQs:
- Why is reliability so crucial in the supply of aero parts?
- Reliability is critical because it directly impacts the safety, efficiency, and operational success of aviation activities. The high standards of aviation safety require that every part functions flawlessly.
- What makes finding reliable aero parts suppliers challenging?
- The main challenges include the vast number of suppliers, the difficulty in verifying the quality and authenticity of parts, and the dynamic nature of aviation standards and technologies.
- How do industry standards influence the reliability of aero parts?
- Industry standards ensure that parts meet specific safety and quality benchmarks. Suppliers adhering to these standards are more likely to provide reliable components.
- Can online marketplaces be trusted for sourcing aero parts?
- While online marketplaces offer convenience and variety, they vary in reliability. It’s essential to conduct thorough vetting and prefer platforms with a proven track record.
- What steps can buyers take to ensure they choose reliable suppliers?
- Buyers should look for suppliers with industry certifications, a strong reputation, transparent quality control processes, and a history of delivering high-quality parts.
Understanding Aircraft Parts Distribution

Overview of the Distribution Landscape
The Ecosystem of Aircraft Parts Distribution
The distribution of aircraft parts is a critical component of the aviation industry’s supply chain, involving a network of manufacturers, OEMs (Original Equipment Manufacturers), distributors, and aftermarket suppliers. This ecosystem is designed to ensure that parts are available globally, meeting the demands of airlines, maintenance providers, and aircraft operators. This section provides an overview of how distribution works, highlighting the roles and relationships between different players in the market. Understanding this landscape is essential for sourcing reliable parts efficiently.
Key Players in the Market
Identifying Reputable Suppliers and Distributors
In the aircraft parts distribution landscape, several key players have established themselves as benchmarks of reliability and quality. This paragraph introduces major OEMs, distributors, and aftermarket suppliers known for their commitment to excellence. By focusing on these reputable entities, buyers can navigate the market more effectively, ensuring access to parts that meet the highest standards of reliability and safety.
FAQs:
- What role do OEMs play in aircraft parts distribution?
- OEMs design and manufacture original parts for aircraft, ensuring that these components meet strict specifications and quality standards.
- How do distributors contribute to the aviation supply chain?
- Distributors act as intermediaries, stocking and supplying parts from various manufacturers to meet the diverse needs of the aviation industry.
- What is the difference between OEM and aftermarket parts?
- OEM parts are made by the original equipment manufacturer, while aftermarket parts are produced by other companies and may offer cost savings or different features.
- Why is it important to understand the distribution landscape?
- Understanding the distribution landscape helps in making informed sourcing decisions, ensuring access to reliable parts, and optimizing supply chain efficiency.
- How can buyers verify the credibility of suppliers and distributors?
- Buyers can verify credibility through industry certifications, customer reviews, company history, and by assessing the transparency and thoroughness of the supplier’s quality control processes.
Criteria for Evaluating Reliable Aerospace Components Suppliers

Quality Certifications and Standards
Ensuring Compliance with Industry Benchmarks
Quality certifications, such as AS9120 and ISO 9001, serve as indicators of a supplier’s commitment to maintaining high standards in their operations and products. This section emphasizes the importance of these certifications in evaluating the reliability of aerospace components suppliers. Suppliers with these certifications have demonstrated adherence to rigorous quality management systems, making them preferable choices for sourcing reliable parts.
Track Record and Industry Reputation
Leveraging Reputation as a Reliability Indicator
A supplier’s track record and reputation in the industry can be one of the most telling indicators of their reliability. This paragraph discusses how long-standing positive feedback, a history of fulfilling complex orders, and endorsements from industry leaders can signal a supplier’s capability to provide dependable aerospace components. It suggests methods for researching and verifying a supplier’s reputation, including industry forums, reviews, and direct references.
FAQs:
- What are the most important certifications for aerospace components suppliers?
- Key certifications include AS9120 for aerospace quality management systems and ISO 9001 for general quality management, among others specific to the aviation industry.
- How does a supplier’s track record affect their reliability?
- A strong track record indicates a history of delivering quality parts on time and meeting clients’ expectations, which is a good predictor of future reliability.
- Can a supplier without certifications be considered reliable?
- While certifications are important, a supplier’s reliability can also be demonstrated through their quality control processes, customer feedback, and operational transparency.
- What research methods can be used to evaluate a supplier’s reputation?
- Methods include checking customer testimonials, seeking feedback from industry peers, reviewing case studies, and analyzing the supplier’s presence in industry-related media.
- Why is supply chain transparency important in choosing a supplier?
- Transparency ensures that the sourcing, manufacturing, and distribution processes meet ethical and quality standards, reducing the risk of counterfeit or substandard parts entering the supply chain.